Industrial & Manufacturing Projects
Build capacity with confidence
- Shave weeks off the project schedule by laying out hundreds of thousands of square feet of conveyance systems, process equipment, complex MEPs, and other trades at the same time.
- Reduce risk of delays from questions and conflicts onsite by driving complete, coordinated design information to the point of work.
- Eliminate schedule risk from rework or change resulting from human error in layout, compounding inaccuracies over large distances, and misaligned phased scopes of work.
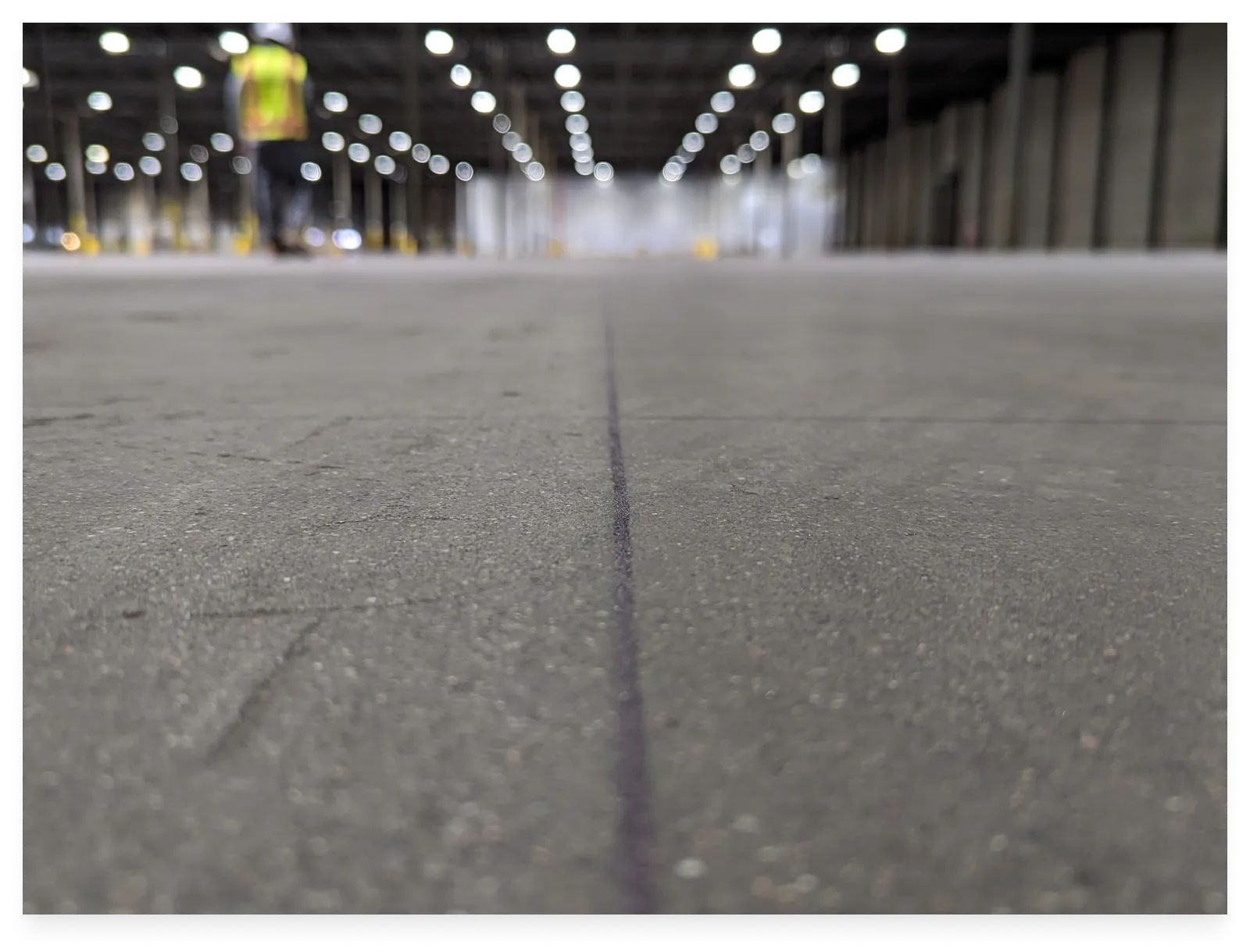
Deliver certainty
- Mitigate schedule uncertainty from custom equipment and new technology by communicating design intent with ultra-high fidelity.
- Don’t let your field teams get stuck waiting on answers. Keep them productive fully-coordinated layout augmented with actionable information, visible to everybody on the job at all times.
- Eliminate schedule risk from human error in layout that compounds inaccuracies over long conveyance runs or big spaces, and misaligned phased scopes of work.

Get Dusty on your next industrial project.
Get what you designed
- Ensure your investment in design and preconstruction translates to ROI in your finished facility by using automated layout to bridge communication gaps.
- Have confidence that construction teams can achieve the accuracy required to implement cutting-edge, high-capacity facilities.
- Connect construction and operations teams to important actionable information by printing equipment identifiers, aisle labels, and QR codes with layout.
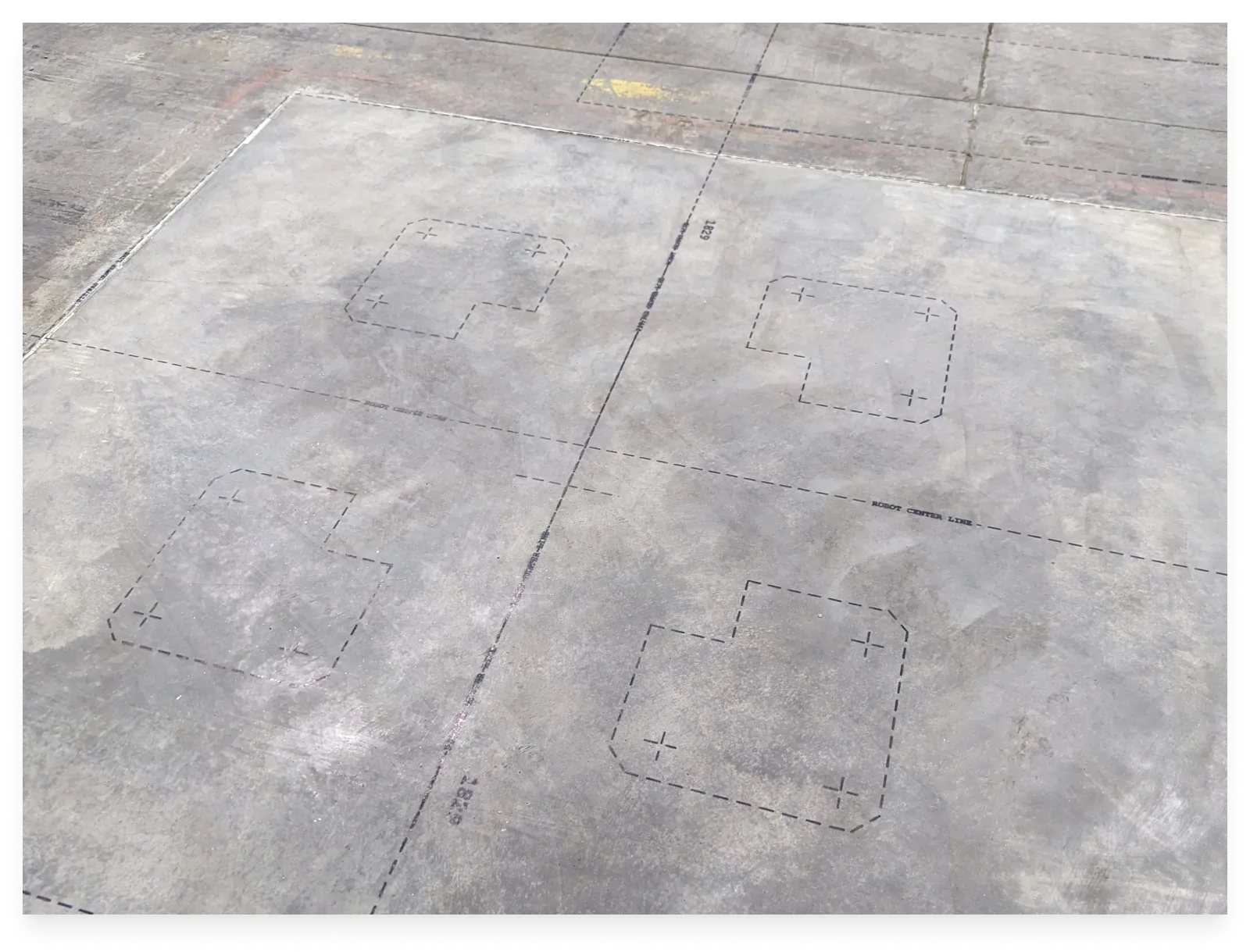
Alston Construction Lays Out Robotic Distribution Center 12x Faster
"On prior job sites, it took roughly 15 days for four people to layout the entire project. With Dusty, we're able to go out there with a single operator and lay out everything in five days."
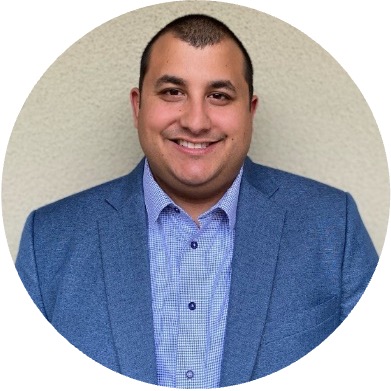
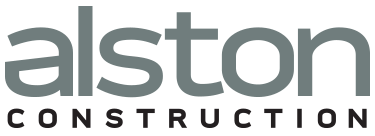
Perform with consistency
- Print multidisciplinary BIM models directly on the jobsite floor at full scale, so that everyone is coordinated and can build accurately and quickly.
- Eliminate problems like skewed conveyance systems, misaligned MEPs, or lack of compliance with OEM specs that result from layout errors that compound over long distances in large facilities.
- Eliminate risk to future projects and achieve highly accurate physical alignment between phased scopes of work, providing strategic flexibility to facility operators.
- Build supply chain resilience with accurate layout that lets crews work around delayed equipment and assemblies.
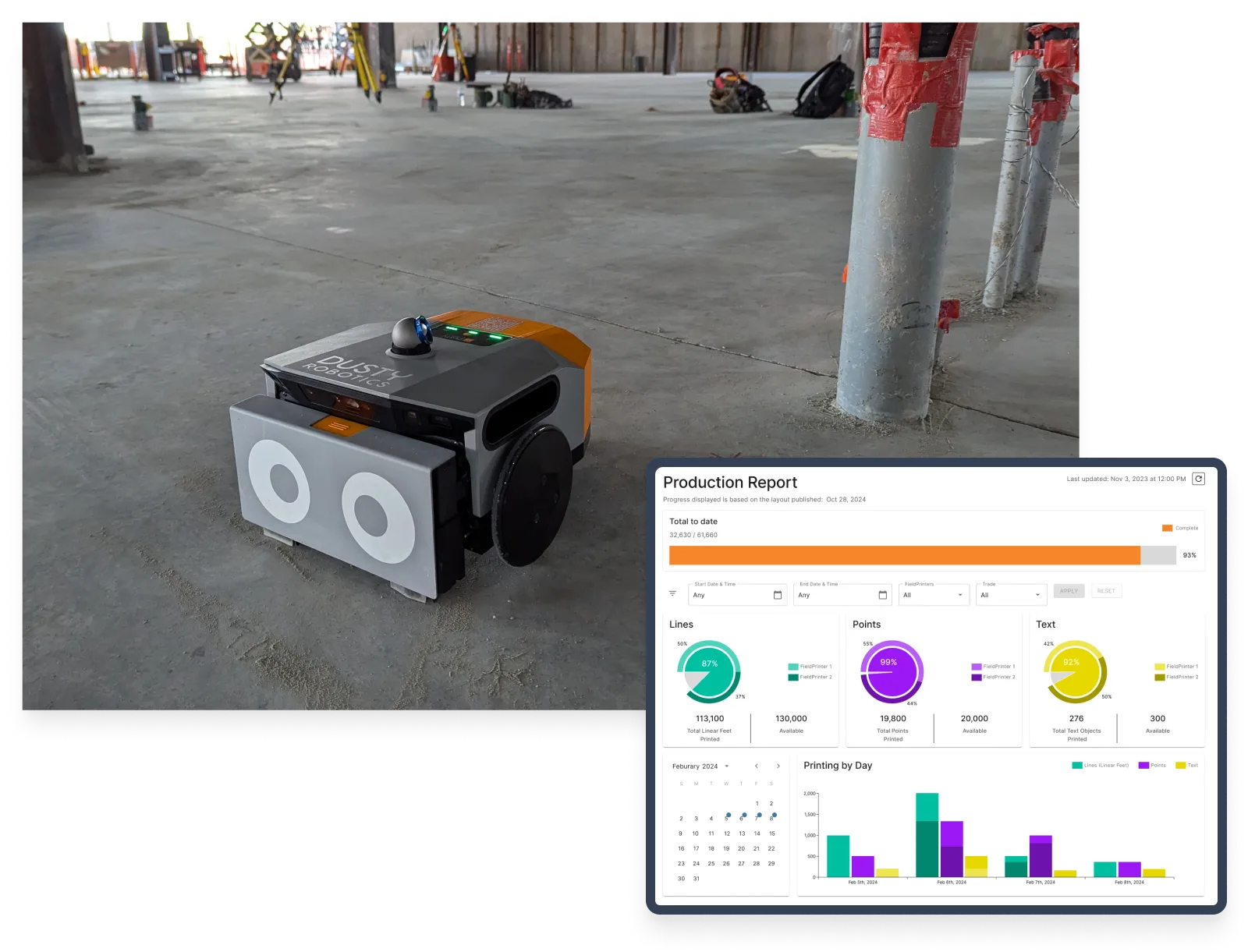
Get off the job faster
- Speed through layout with 10x faster productivity than traditional methods.
- Set crews up for high productivity by eliminating the information gap between VDC and the field.
- Eliminate time-wasting conflicts between trades. Stack cooling, power, data, and other trades for installation efficiency.
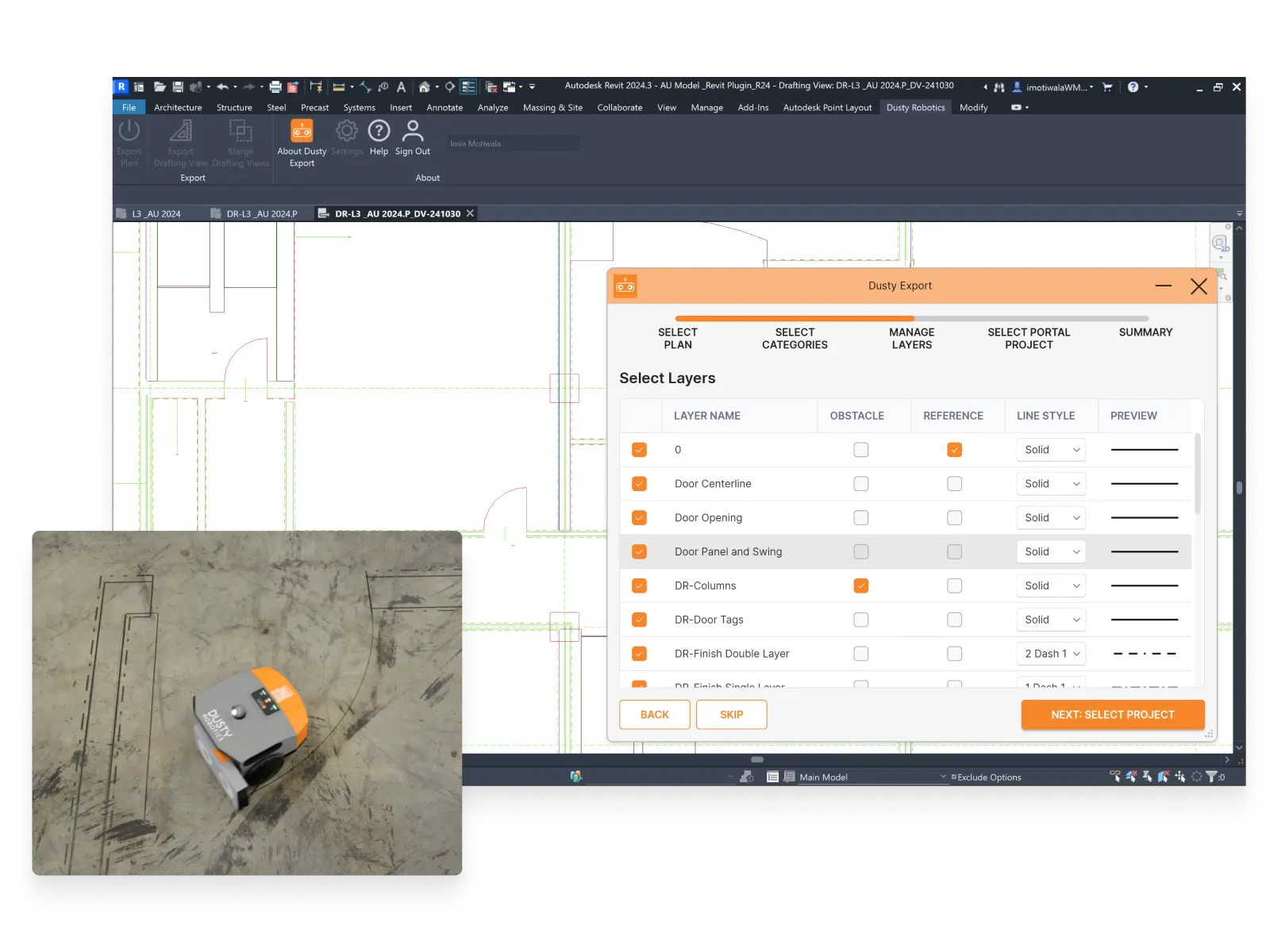
See Dusty on manufacturing facilities.
Frequently asked questions
Automated layout in industrial and manufacturing construction uses robotic technology to precisely mark design plans onto the jobsite floor. This eliminates manual errors, ensures alignment across multiple trades, and speeds up project execution. By integrating BIM models into the field layout process, automated solutions improve accuracy for facility owners and contractors working on manufacturing plants, distribution centers, semiconductor facilities, pharmaceutical plants, and other industrial projects. This reduces rework, enhances coordination, and minimizes construction delays. Dusty Robotics’ automated layout technology helps teams achieve high-precision execution while accelerating project timelines.
Industrial and manufacturing projects require extreme accuracy, as even small layout errors can lead to misaligned equipment, inefficient workflows, or noncompliance with industry regulations. Automated layout ensures accuracy by printing full-scale, model-based details directly onto the job site floor. This eliminates human measurement errors that can compound over large distances, particularly in facilities with extensive conveyance systems, cleanroom environments, or complex MEP installations. Automated layout is ideal for projects like logistics hubs, high-tech manufacturing plants, automotive production facilities, and energy infrastructure projects where precision is critical. By reducing rework and ensuring exact placement, contractors can confidently meet project specifications and performance requirements.
Automated layout significantly reduces layout time compared to traditional manual methods by up to 10x. This allows contractors to accelerate field production in large-scale industrial projects such as semiconductor fabrication plants, pharmaceutical manufacturing facilities, and heavy industrial plants. By eliminating delays caused by design clarifications or field adjustments, automated layout helps teams stay on schedule and prevents costly overruns. Facility owners benefit from faster project completion, allowing them to start production or distribution operations sooner. Additionally, automated layout reduces the number of person-days required for layout and freeing up skilled trades for higher-value work.
Automated layout is essential for construction projects in facilities that remain operational while undergoing upgrades, retrofits, or expansions. In active manufacturing plants, pharmaceutical facilities, and distribution centers, precision is critical to avoid disrupting existing workflows, utilities, and production lines. Automated layout ensures that modifications—such as new equipment installations, MEP system upgrades, or process expansions—integrate seamlessly with the existing infrastructure. By providing exact placement markings with minimal disruption, contractors can maintain productivity while executing high-accuracy work. This technology reduces downtime, enhances coordination between trades, and ensures projects stay on schedule without interfering with daily operations.
Rework in industrial and manufacturing construction often results from inaccurate layout, misaligned structural elements, or incomplete design communication. Automated layout minimizes these risks by printing precise, real-time markings that match the original BIM model, ensuring trades can install process equipment, structural supports, and utilities exactly as designed. This is particularly valuable for large-scale projects such as food processing plants, advanced manufacturing facilities, and pharmaceutical facilities, where precision impacts production efficiency. Reducing rework not only prevents costly delays but also minimizes material waste, supporting sustainability goals in industrial construction.
Dusty Robotics’ automated layout technology is ideal for a wide range of industrial and manufacturing projects that require high accuracy and efficient execution. These include:
- Manufacturing Plants: Semiconductor fabrication facilities, automotive factories, aerospace production sites, and advanced manufacturing centers.
- Distribution & Logistics Centers: High-volume fulfillment centers, cold storage warehouses, and automated distribution hubs.
- Pharmaceutical & Cleanroom Facilities: Biotech labs, pharmaceutical manufacturing plants, and semiconductor cleanrooms requiring ultra-precise layout.
- Heavy Industrial & Energy Facilities: Oil refineries, chemical processing plants, power generation sites, and renewable energy infrastructure.
- Food & Beverage Processing Plants: Facilities with extensive process piping, specialized equipment, and sanitary requirements.
By ensuring layout precision, reducing schedule risk, and improving coordination across trades, Dusty Robotics supports faster, more reliable execution for these complex industrial projects.
Dusty Robotics’ automated layout technology connects BIM workflows to field operations by translating digital models into full-scale site markings. This integration ensures that complex design elements—such as process equipment placements, high-density racking, and intricate MEP systems—are installed accurately in manufacturing plants, logistics centers, and industrial warehouses. By providing clear layout guidance, Dusty Robotics eliminates misinterpretations and streamlines coordination between VDC teams and field crews. The addition of QR codes and equipment labels further enhances communication, making it easier for teams to access key model data. This seamless BIM-to-field collaboration improves efficiency, accuracy, and overall project success.
Want to learn more?
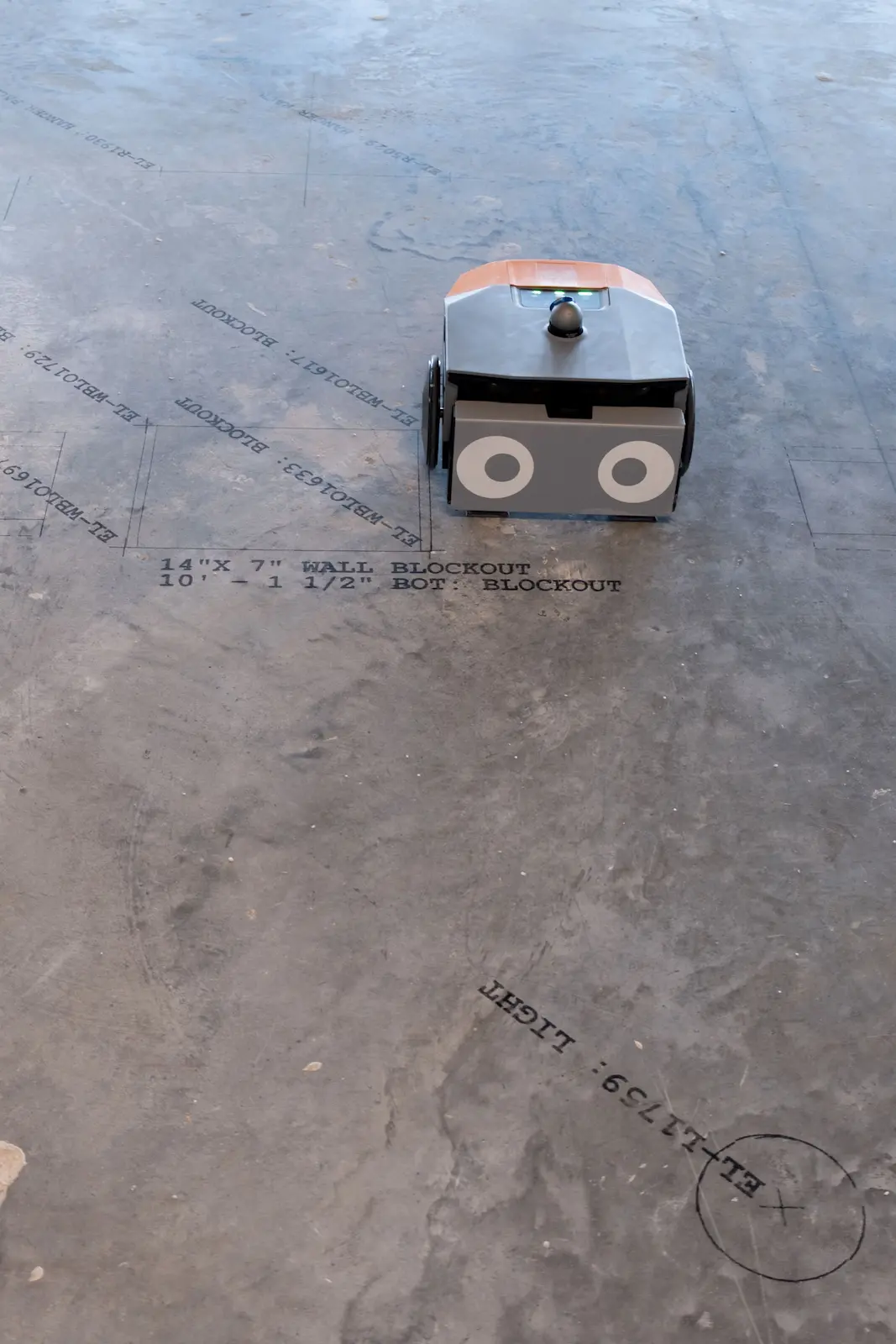
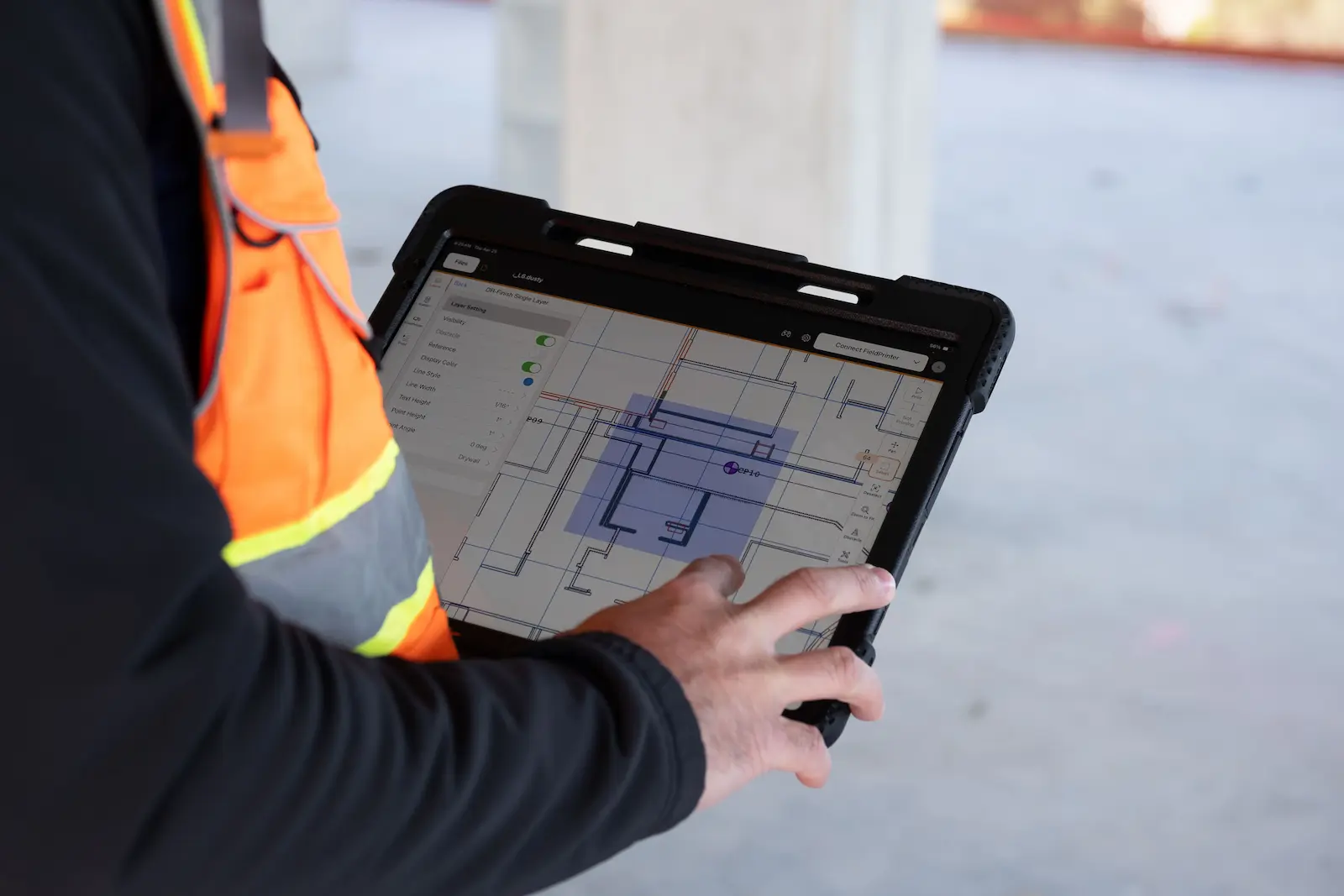
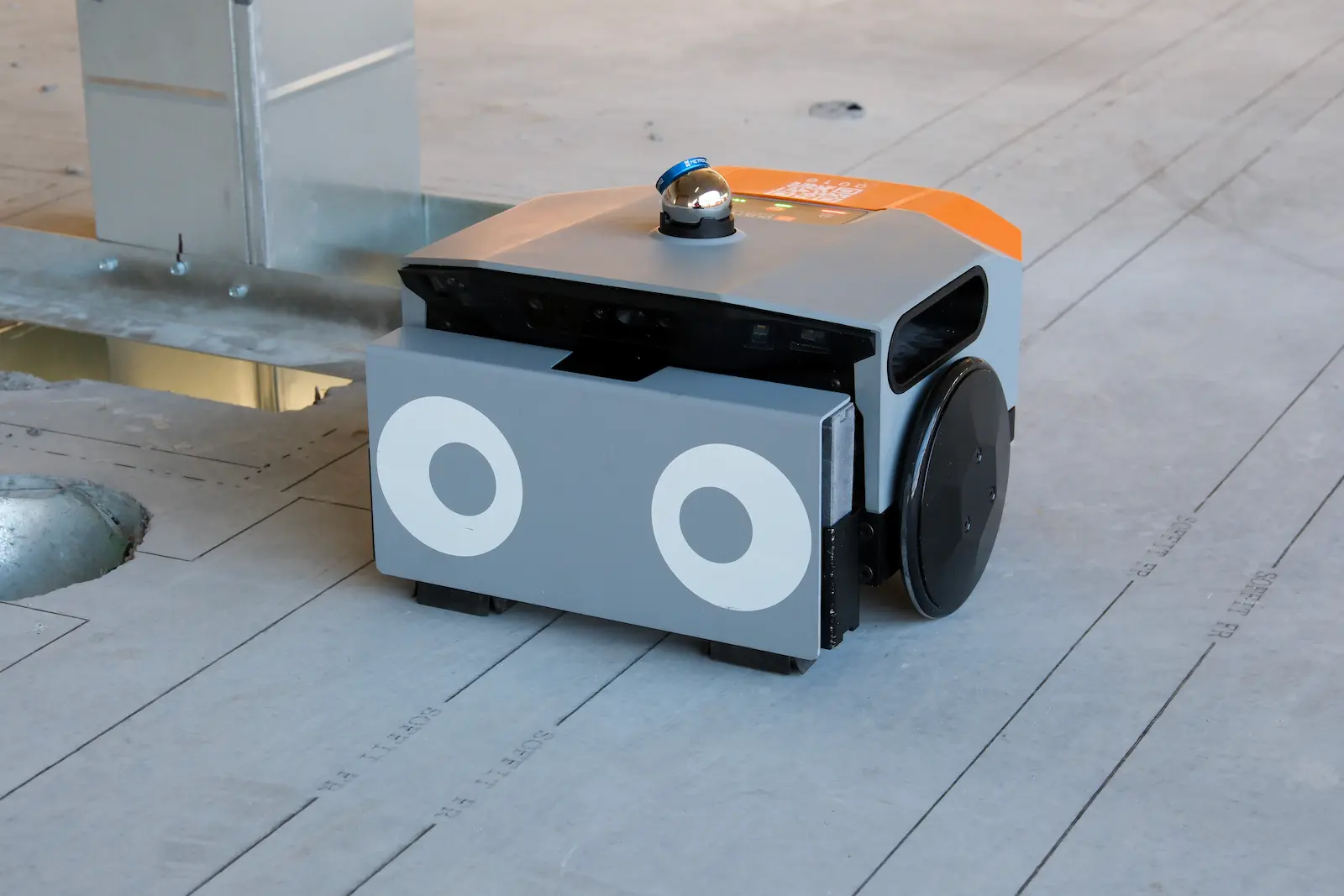