Align is a global provider of technology infrastructure solutions spanning four lines of business: Workplace Technology, Data Center Design & Build, Migrations & Cloud, and Managed Services with offices around the country and in London.
Data centers house large numbers of computer servers and related infrastructure designed to store, manage and process vast amounts of data. Usually built within a warehouse-like structure, they are the powerhouse behind digital operations such as cloud computing, AI, online services, enterprise networks and big data analytics.
Data center builds are an intricate and meticulous process; from the cabling to cooling systems, they count on the accuracy of layout for optimal performance. Even minor oversights can result in both immediate and future issues.
Align adopted Dusty Robotics’ technology to improve their layout processes, leading to significant benefits in speed, accuracy, coordination, safety, and insurance cost savings.
Dusty Delivers a Faster Layout Process
Laying out the placement of IT racks is imperative to a data center project. David Donato, Director of Data Center Design and Construction, says Dusty Robotics is transforming the layout process at Align.
“Imagine a parking garage without any parking lines painted. You wouldn’t know where to park. It’s the same with IT racks in a data center. The floor markings and grid we paint assigns the racks a designated spot,” Donato says. “Using Dusty Robotics, we can create these precise layouts quickly and accurately.”
Before Dusty, a typical data center layout could take up to a week with a crew of 20 people. The back-breaking process involved employees on their hands and knees on concrete floors drawing out IT rack placements with a Sharpie.
The layout process for Align has significantly improved since they started using Dusty Robotics.
A recent project using Dusty completed a layout on a 15,000 square foot room in one day using only two people. That's a reduction of 784 person-hours, allowing no fewer than 18 people to put down their Sharpies and get back to installing.
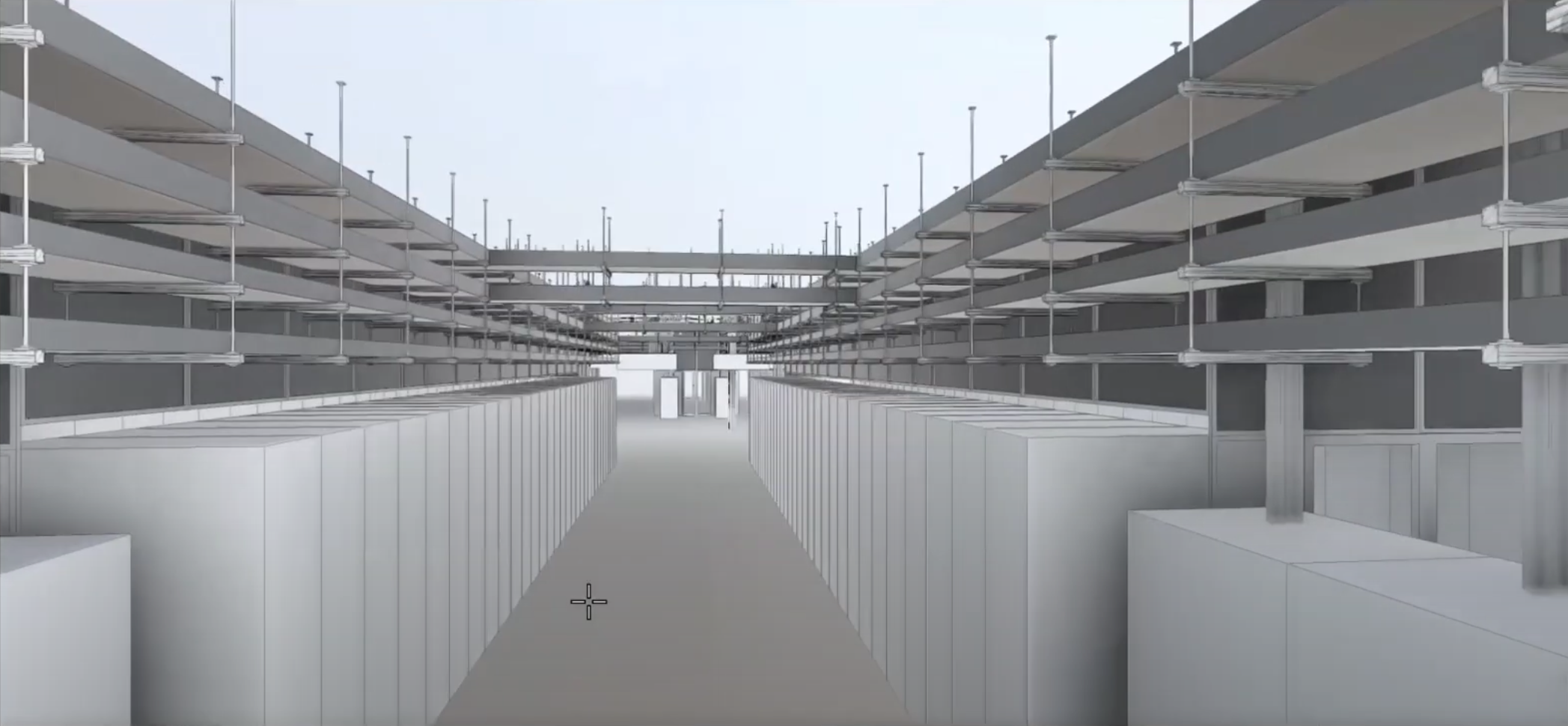
“With Dusty Robotics, we were able to reduce the time required for layout from a week to just one long day. What once took 20 people now only requires two,” says Donato. “The efficiency gains have been incredible, allowing us to complete projects faster and with fewer resources.”
Align was also able to incorporate Dusty Robotics into the labeling process for grid sections, achieving even greater efficiencies. Traditionally, Align’s scope of work includes manually affixing barcode labels to the floor at each rack location. The barcodes can be scanned to quickly retrieve information about the exact location, equipment, and specifications for that particular section, streamlining operations.
“The integration of barcode labels into our layout process has transformed how we manage and track each section of the grid. These labels provide precise, unique identifiers that streamline our workflow and enhance accuracy in our data center layouts,” Donato says.
Align Achieves More Accurate Layouts with Dusty
Data center builds require highly accurate layouts due to tight tolerances with prefabricated components.
Dusty Robotics uses an advanced laser tracking system to ensure accuracy, eliminating the human error that can occur with manual methods. And because the layout that Dusty prints comes directly from the model, Align is able to seamlessly translate digital designs into real-world layouts on-site.
“With Dusty Robotics, we were able to efficiently install 384 racks in six rooms, totaling 2304 racks,” Donato says. “The precision and speed of Dusty’s technology allowed us to complete the layout and installation accurately and quickly, ensuring everything fit perfectly.” Dusty achieved the 1/16” tolerance necessary to install the prefabricated materials.
Dusty Robotics can also handle irregular shapes and uneven surfaces with accurate measurements even in challenging conditions. This is particularly important for rooms with out-of-square columns or uneven floors.
“In one job there were issues with support columns that were supposed to be square but were actually trapezoid-shaped, rhombus-shaped—everything but square. The angle the column faced could vary by five degrees, making precise measurements a challenge,” Donato says. “Dusty Robotics helped us achieve the necessary precision, ensuring our layout was accurate despite the irregular shapes of the columns.”
.jpeg)
Dusty Promotes Better Coordination with Subcontractors
Data center builds require multiple trades and subcontractors to coordinate on the project. This can make layout complicated, as different crews might measure from different reference points, causing discrepancies.
Dusty Robotics enhanced coordination by delivering a single layout for all trades to follow. This enabled seamless trade stacking and improved overall efficiency among different subcontractors.
“The equipment and components, such as containment systems and electrical enclosures, are prefabricated off site, so dimensions are fixed. That means the layout has to be spot-on,” Donato says. “The level of precision with Dusty has significantly reduced errors and rework.”
Donato says using new technology on the data room build made subcontractors apprehensive at first. "It was different than they have done before, but once we explained how Dusty would work, everyone signed up pretty quickly,” Donato says. “Electricians on the project appreciated the accurate layout provided by Dusty Robotics, which helped them install their systems more efficiently.”
Dusty Helps Make the Project Resilient to Supply Chain Challenges
When equipment delivery delays happen in the project, Dusty’s layout can be counted on for the accuracy to move forward. Align was able to continue working when supply chain delays could have brought the project to a standstill.
“One piece of ledger was delayed by almost three months. We had to install all of the supporting infrastructure above it, including the pipes coming down from the ceiling, two months before the gear arrived,” Donato says. “Without Dusty, we wouldn’t have felt confident about the accuracy, and any misalignment could have resulted in significant rework.”
Align Creates a Safer Work Environment with Dusty
Using the traditional methods, layout crews experienced long days on their hands and knees for an extensive amount of time. It led to the potential for repetitive motion- and fatigue-related injuries.
Dusty saves employees from the exhaustion of extended hours and the pain of awkward positions necessary for manual layout.
Align took the safety improvements to their insurance carrier, resulting in discounts and reduced workers’ compensation costs.
“We improved our safety program and were able to secure premium discounts in our workers’ comp insurance thanks to Dusty Robotics,” said Donato. “With employees no longer working on their hands and knees, we were able to eliminate a fatigue management plan and demonstrate reduced risk exposure, securing a premium discount.”
Dusty Robotics is now a permanent part of Align’s layout process, integrating into the design workflow, enhancing efficiency and consistency. Thanks to the partnership, Align is better equipped to quickly produce large-scale data center projects for demanding clients.
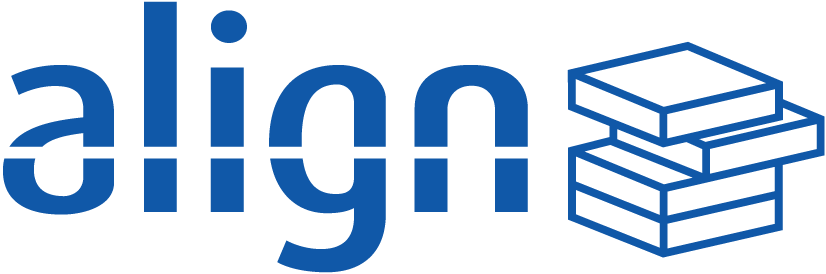
Align uses Dusty Robotics as their multi-trade automated layout solution to accelerate large data center builds where schedule pressure is high and tolerances are tight.
Interested in learning more about the
Dusty FieldPrinter?
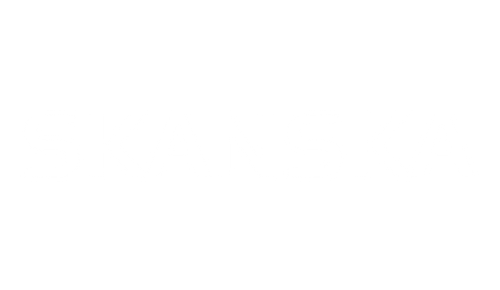
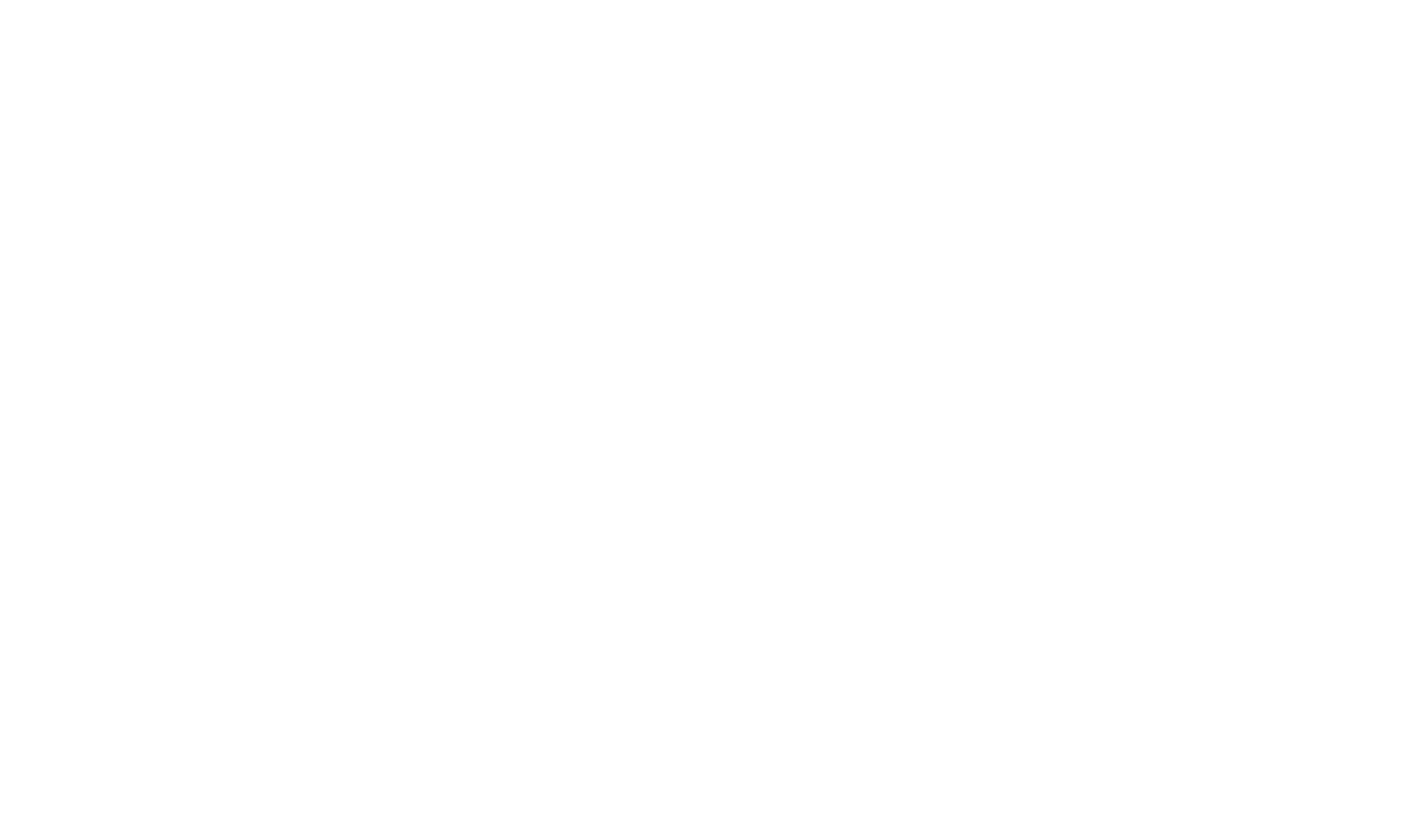
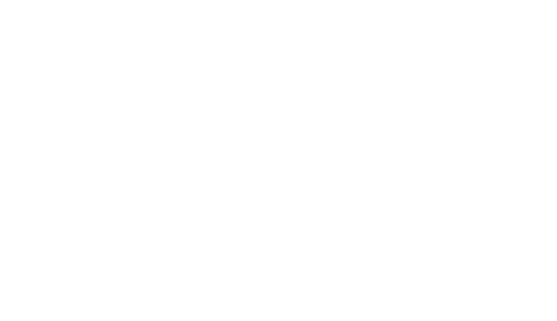
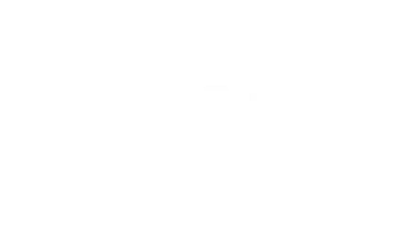
.png)
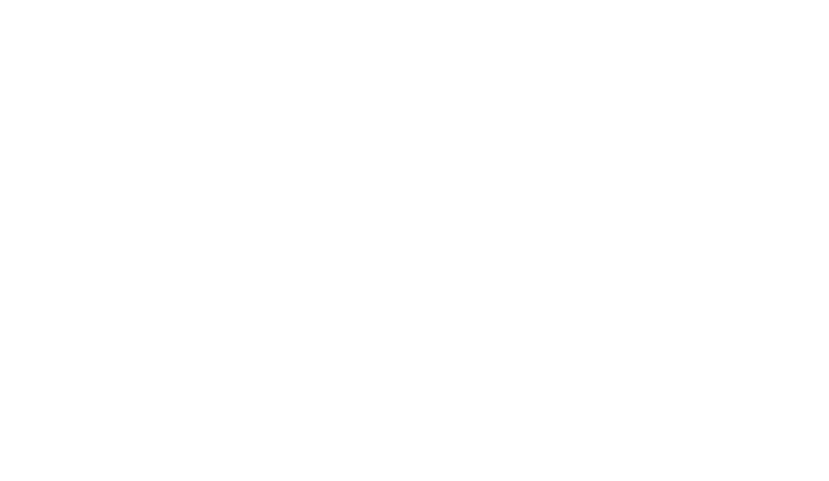