Laying out our path
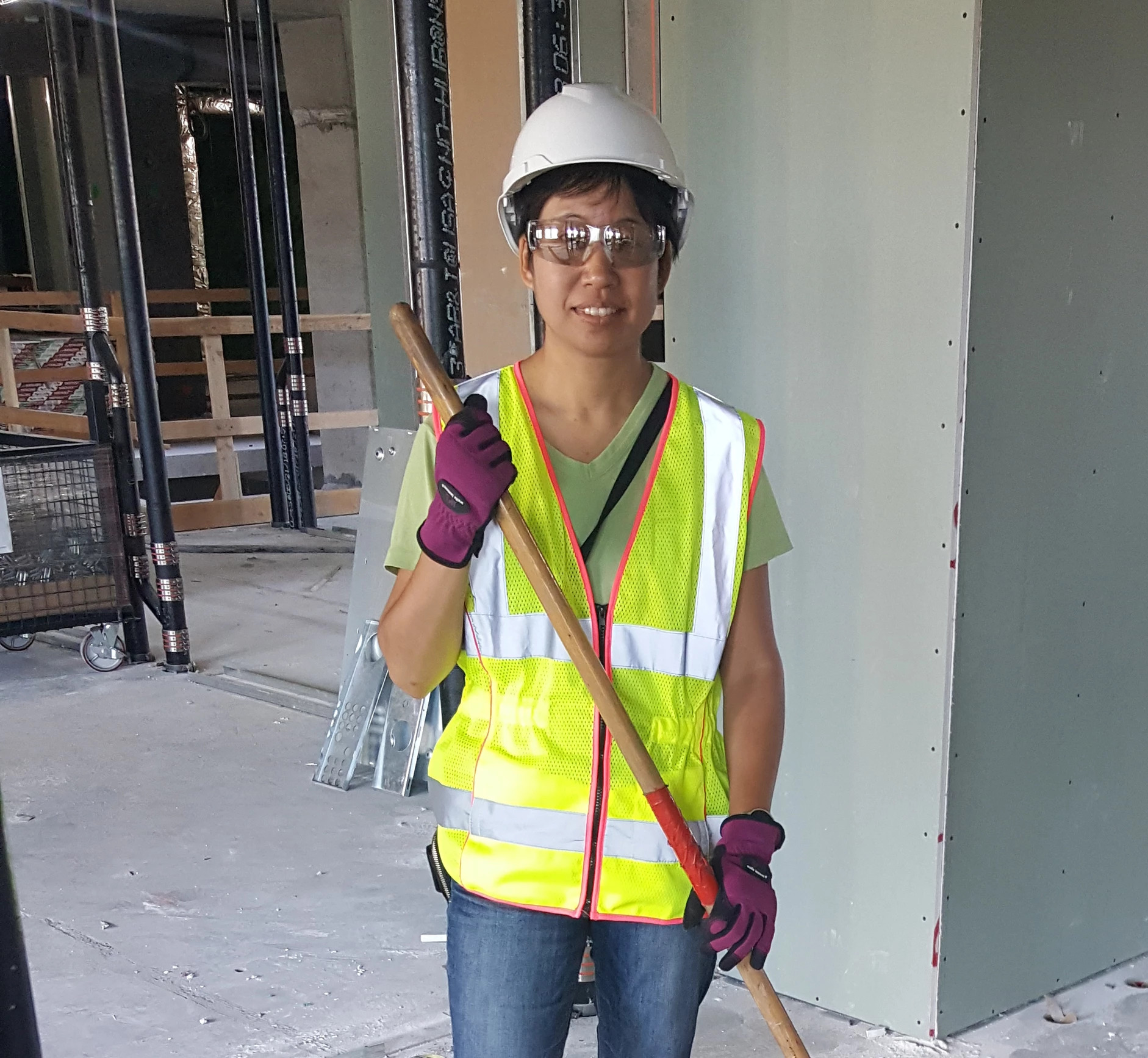
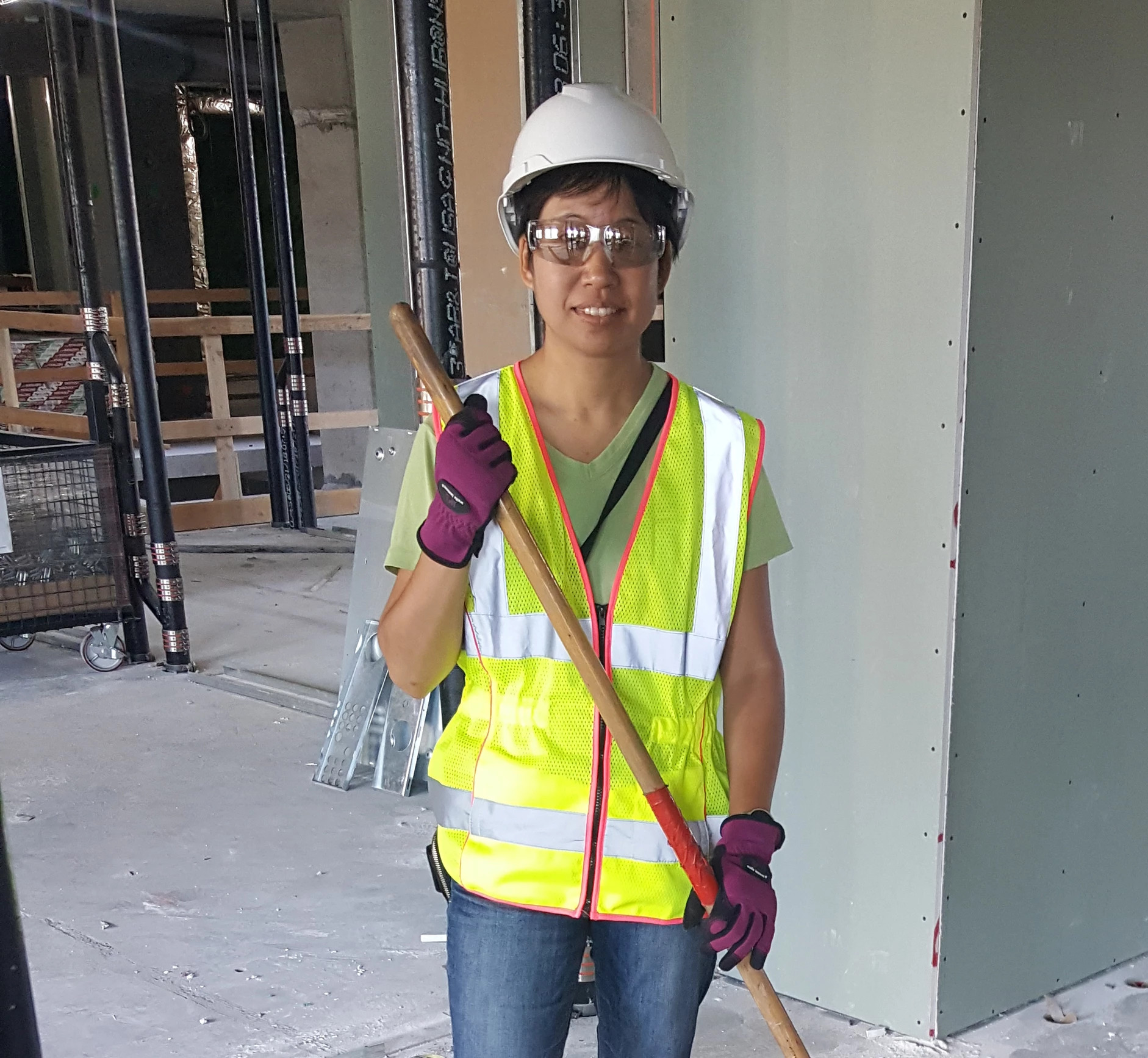
While we were mapping out the construction robotics market, we also spent several months walking construction jobsites and talking to everyone we could about the challenges in the industry and where robotic automation could fit in.
One of the most common mistakes startups make is building a product nobody wants. I wanted to avoid that mistake at Dusty, so I asked open-ended questions and tried to understand the underlying pain points in each person’s job role. Not knowing much about the industry myself, I strove to keep an open mind and see firsthand what the construction process was like and where automation was needed. I wanted our customers to tell us what we should build.
The customer discovery process was very frustrating at first. Each person I talked to had different ideas about automation, based on their own unique experience. I also learned that many people weren’t comfortable suggesting product ideas, perhaps because they didn’t know what is possible and didn’t want to sound ignorant. So I quickly shifted my line of questioning to focus on gathering feedback around a small number of candidate product ideas, which reflected pain points I’d heard from multiple sources.
Of those ideas, the first one to survive all of our tests was jobsite cleanup. Every jobsite needs to be cleaned up. It could be done overnight, taking advantage of a second shift to get work done while people slept. It’s easy to describe: just imagine a ruggedized Roomba for the construction industry. A small but significant percentage of each project’s budget is allocated to cleanup.
Cleanup isn’t on the critical path, but it was the best idea we had at the time. We decided to move forward with it, even though we still had some reservations. We visited several jobsites and talked to superintendents about how they kept their sites clean. We even spent a Saturday doing cleanup ourselves, pushing debris around with brooms and measuring the volume of particulate matter our robot would need to handle. And then we decided to spend a full shift on one particularly busy site, shadowing the workers doing cleanup and tracing the flow of garbage as it moved through the site.
It was during this shift that we identified the opportunity that will define Dusty’s business. As we walked the site, we observed people consulting printed plans, using tape measures, and debating where to place certain features. We saw people using handheld calculators, trying to add up dimensions. When we examined the floor, we saw a multitude of lines and symbols marked on the ground, denoting locations of interior walls, ducts, and pipes. Layout was all around us.
I started calling up those construction professionals I’d talked to earlier, to ask about layout. How is layout done today? How important is it for layout to be accurate? How valuable would it be if we could automatically mark those lines on the ground, using a high-precision robot?
The response was immediate and overwhelming. Layout is fundamental to every single construction project, because it specifies what is to be built in a way that every worker on the site can interpret and build on. Mistakes made during layout can cause structures to be built in the wrong place, which must be subsequently torn down and rebuilt at significant expense. In some cases, layout is even on the critical path; a project can become delayed if the necessary crew is not available at the right time to lay out a floor.
We also imagined that automated layout could be much more useful than what is currently laid out on sites today. Much of the information stored in the BIM model (the CAD drawing that specifies what is to be constructed) never makes it onto the site. Information such as dimensions, part numbers, elevations, and even QR codes could be extracted from the BIM model, and placed on the ground where everyone walking the site will see it. Automated layout would bridge the gap between BIM and the field, ensuring all workers are always building off the latest set of construction documents.
At the same time, Phil did a series of calculations to determine whether it would be feasible to build a layout robot. Human layout crews are precise to within 1/16”, or less than 2mm. A layout robot would have to be incredibly accurate -- at least an order of magnitude more accurate than the best available mobile robots today. Phil’s analysis revealed that it would be challenging, but we could do it.
I had just gotten off a call with a general contractor who was excited about layout automation. It felt like we were on to something, and that we could build it. Phil and I looked at each other and said, “This is it. Let’s do layout.”
What do you think of our journey so far? Let us know in the comments below. Stay tuned to follow our progress.