The Future of Construction: Year 2030 Predictions
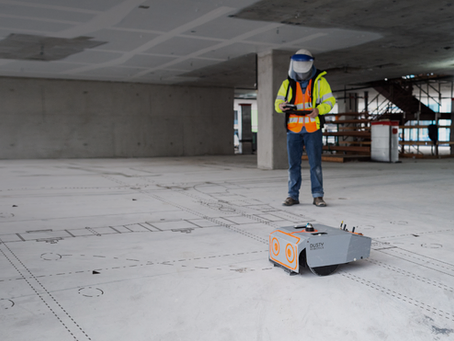
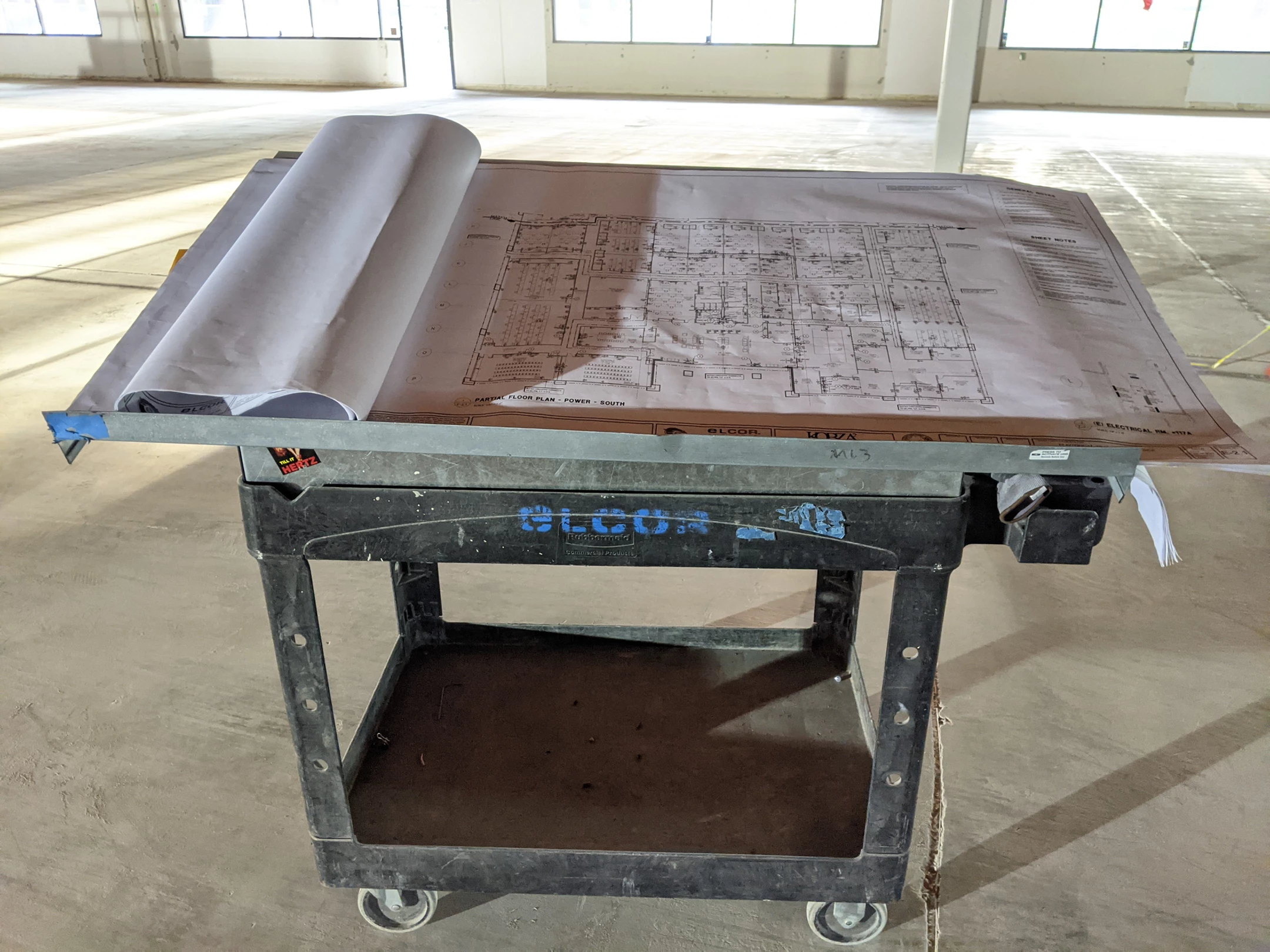
Every time I’m out on a construction site I pay attention to the paper. On every floor where trades are at work there are typically a few tables piled high with shop drawings. These are the blueprints for the building under construction, and provide all the information needed for crews to manufacture the building.
Unlike factory manufacturing, in construction each building is a unique snowflake. And the vast majority of work is performed by skilled crews working in tight coordination on schedule. That makes information flow critical to the success of the manufacturing process.
But with information disseminated via paper plans, manual observation, and phone calls, mistakes get made. This information-driven manufacturing process is analog and error-prone. Digitization will help. But how do we introduce digitization into the controlled chaos of a construction site, with hundreds or thousands of workers each assembling a different piece of the product every day?
Layout automation is the entry point. Layout is the critical piece of information that tells crews what to build, and where it goes. Today, layout is done with measuring tape and chalk lines based off of paper plans. Layout is a critical-path step, with cascading effects throughout the project. By the time mistakes are discovered, the cabinets don’t fit and you have to decide whether to re-order the cabinets or move the walls.
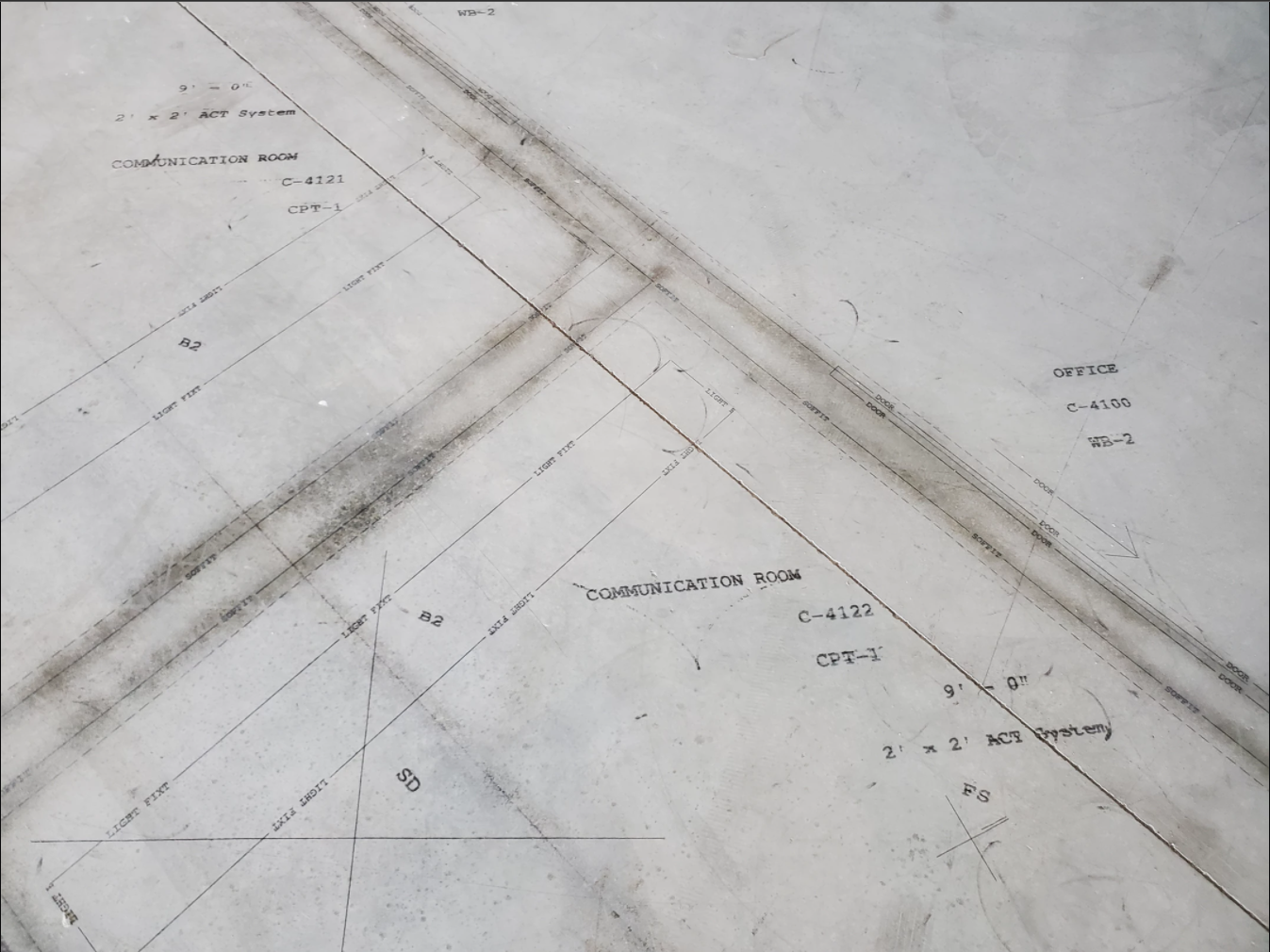
The next step in layout automation is what we are calling “enhanced layout”. Enhanced layout takes additional information from the digital models and brings it out to the construction site alongside traditional layout. For example, on one project we printed room legends at the entrance to every room. These room legends could include information such as room name, number, ceiling type and height, or even paint colors and floor finishes. On another project, we printed complete mechanical shop drawings on the floor, taking all the information from those paper plans and rendering part numbers, dimensions, heights, and shaft runs on the floor directly underneath where those components were to be installed. Within the first few minutes of printing these shop drawings, our client had already identified one conflict where the existing structure would clash with the proposed duct installation height.
Enhanced layout is like having IKEA instructions for construction. This additional information eliminates mistakes due to not having the right information at the right time, and makes the manufacturing process almost foolproof.
But mistakes still happen, even with correct layout. One of our clients told me about a mistake on one of their projects where the wrong type of conduit was delivered to a job site. The electricians dutifully installed them all, and then had to change out miles of conduit once the mistake was discovered.
Digitizing the work done on the project will catch these mistakes sooner. But where do we start? Imagine if workers have an app that lets them scan in the barcode from the part they’re installing, then scan in a code on the floor (which Dusty has printed). Instantly we have a data point about who installed what, and where. If the part number doesn’t match the submittal, the error is caught immediately before the part gets installed.
This information feeds into a digital twin of the building, giving project managers a real-time view of the work being done in the field. They can instantly see where work is slowing or stopped, identify and react to issues as they arise, or even head them off before they snowball. Simply being able to see this information live will eliminate a whole class of time wasted on phone calls and information gathering.
But digitization goes beyond progress monitoring and work verification. Digitization of work done on the site enables data-driven analytics over the entire construction process. For example, what if manufacturer A’s parts require 20% more installation time compared to manufacturer B’s? This information feeds back into the design process, enabling teams to optimize the design using data from actual manufacturing processes.
This is our vision for where the construction industry will be by 2030. Digitization of work in the field turns construction to a data-driven manufacturing process. These productivity enhancements to the built environment are the only way we will meet the world’s demand for housing and infrastructure into the mid-21st century.