How to Shorten Construction Schedules
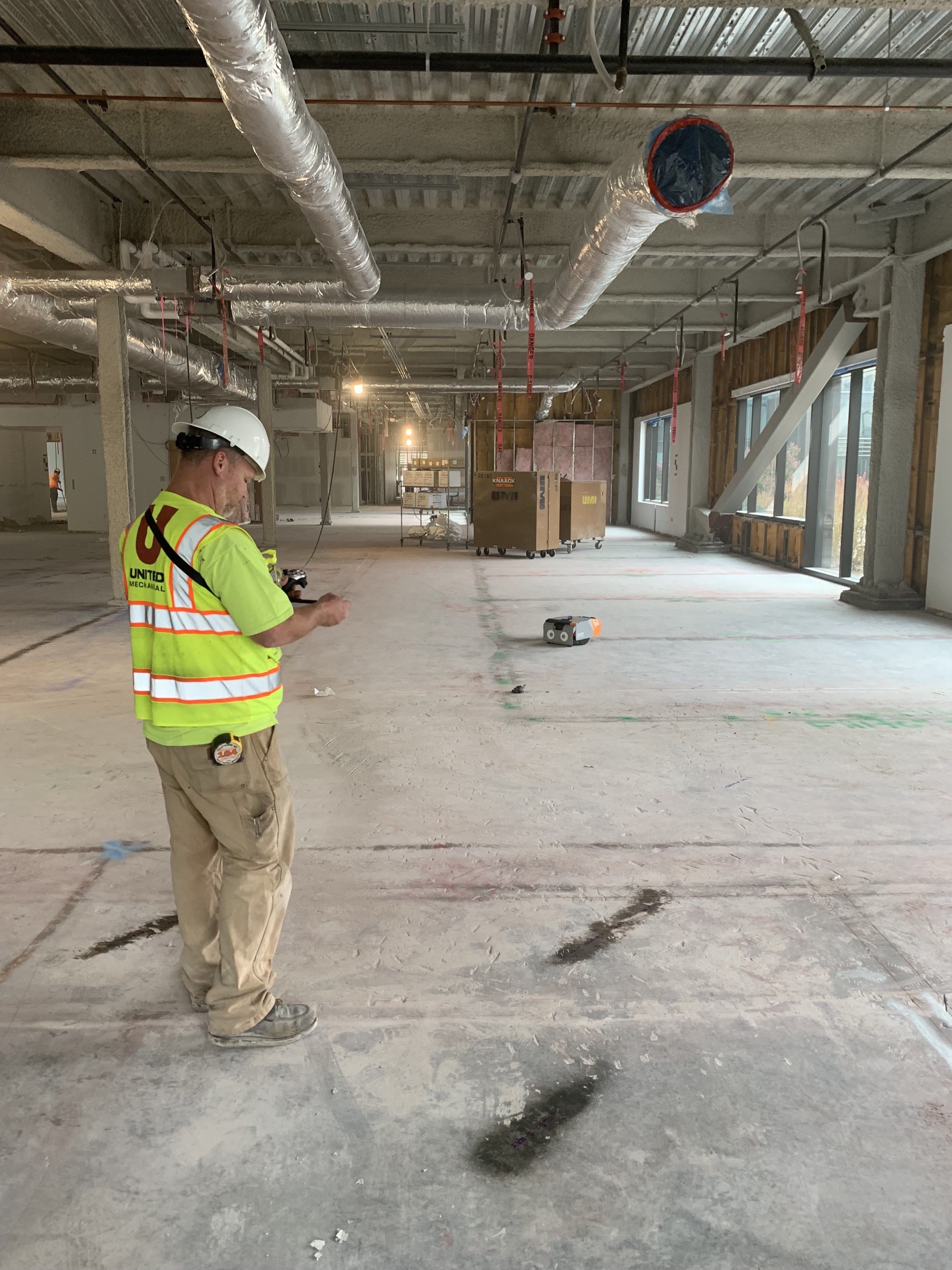
Maintaining a construction schedule is notoriously difficult, and project delays happen all too often in the construction industry. With a worsening skilled labor shortage, complex planning requirements, and error-prone manual workflows, a lot can go wrong. Whether a design conflict occurred or a mistake was made during layout, delays in a construction schedule negatively impact everyone involved. Improving construction requires both eliminating those avoidable delays and compressing routine schedules.
Read on to learn the top reasons for construction delays and tips to shorten your construction schedule.
Delays in construction schedules can happen for various reasons both large and small. Here are the top causes of delays in the construction industry today.
- Difficulty Accessing Skilled Labor
- Budgeting Issues
- Missing or Incorrect Data
- Mistakes & Conflicts
- Slow Communication & Approval
- Poor Weather
Any of these problems can derail a construction schedule, which leads to increasing budget and scheduling issues throughout the project.
What are the Impacts of Delays in Construction Projects?
Delays are bad for business. Customers expect companies to stay true to their word and follow through with any agreed-upon timelines, especially when the timelines determine financial outcomes. Construction schedules are a key factor in estimating an overall project budget because the cost of labor is tied directly to the number of man-hours required to complete a job. Extending this time frame significantly increases labor costs. Further, delays related to layout or installation mistakes require additional and possibly redundant material costs. With numerous trades involved, there’s also no guarantee that the new schedule will align with everyone’s availability, resulting in even longer delays. Avoiding delays in the first place is critical to preventing a cycle of frustrating and expensive delays that can sink a project. Let’s review the top tips to shorten construction schedules and keep your project on track for success.
5 Tips to Shorten Construction Schedules
Overcoming delays can seem impossible, but they’re avoidable with the right tools and processes in place. Here are the top 5 tips for avoiding delays and compressing your construction schedule.
- Investing in BIM
Building information modeling (BIM) is an intelligent software modeling process that allows architects, engineers, and trades to collaborate on a construction project simultaneously. Everyone involved in the planning has their own “view” of the 3D model, providing a centralized and common dataset that can be modified in real-time. With visibility into the prospective changes, teams are enabled to detect and resolve conflicts earlier in the design process. This results in fewer issues to resolve in the field, expediting construction time and saving money. In addition, BIM scheduling and budget estimates can be established across all trades to prevent projects from incurring delays or unexpected expenses.
Investing in BIM is the first step in designing accurate construction plans, and using BIM-driven layout is the next step for maintaining accuracy all the way through construction.
- Using BIM-Driven Layout
Layout is a time-consuming, error-prone, and high-risk process when done manually. Each floor of the construction site must be kept clear for the duration of layout for all trades, creating a bottleneck in the construction schedule. Manually measuring and marking reference points frequently results in errors, especially when aligning layout across trades such as drywall (framing), mechanical, electrical, and plumbing (MEP). If those errors aren’t identified immediately, they can lead to expensive and tedious rework that consumes more time on the construction schedule.
In addition, layout is the most physically demanding part of a foreman’s job, bending down and marking the floor thousands of times a day. This manual process results in workplace-related injuries that not only derail construction schedules but also shorten the lifespan of these valuable workers.
Dusty Robotics’ FieldPrinter autonomously prints all trades’ layout directly onto the construction site surface. This prevents the need for foremen to mark the floor, reducing workplace injuries. With 100% accuracy to the BIM model, robotic layout eliminates errors while compressing existing construction schedules. For instance, Dusty’s FieldPrinter is 10x faster than manual methods and can complete accurate layout across all trades in a manner of days, not weeks. Installation is able to start sooner and the project can finish weeks ahead of schedule.
- Listening to Worker Feedback
Workers are in the field day in and day out. They have the most up-to-date knowledge of a project’s progress, including potential red flags about conflicts, data inconsistencies, delays, or scheduling issues. Likewise, workers are a valuable source of information. Listen to what they have to say, especially if they have concerns about project timelines. Often, if issues are addressed early on, they can be resolved before they start to impact longer-term scheduling and budget concerns. By listening to your team in the field and being receptive to feedback, you can fix issues that would otherwise have resulted in scheduling delays, such as compliance documentation, job build information, subcontractor scheduling, and more. Part of listening to worker feedback is establishing clear communication protocols.
- Streamlining Communication
Strong communication is an ongoing challenge for construction projects, and poor communication is behind almost half of all rework. As inherently complex projects with numerous professionals involved, there’s room for miscommunication at every step of the process. Whether it’s from an owner, client, architect, engineer, or contractor, having a clear communication strategy in place is critical to avoiding delays, conflicts, and rework.
Technology is helping to streamline communication by providing a single source of truth for all parties involved in a project. Using BIM allows architects, engineers, and trades to access the exact same design information, collaborating in real-time for changes and updates. This helps identify issues earlier on and provides a clear audit trail in case a conflict does arise. Likewise, BIM-driven layout ensures that all trades are working off the same information, leading to less finger-pointing and more collaboration on-site. With strong collaboration, communication, and visibility into real-time changes, projects can be completed sooner and with fewer frustrations.
- Standardizing Workflows
Job sites quickly become disorganized when there’s no standardized workflow. Each project team and field crew has its own way of doing things, and variances from job to job can cause some jobs to fail while others succeed.
BIM-driven layout ensures that all field crews adhere to a common schedule and workflow, ensuring that the same information is always made available to the field crews, and forming the basis of a standardized field install workflow which will create consistent outcomes from project to project.
Establishing standard routines improves the organization and quality of a job site, as well as the ability to stay on schedule. Other areas of standardization include creating standard routines for sorting and organizing tools, cleaning and sweeping the job site, and storing materials. By routinely meeting for a team huddle in the morning and communicating these expectations, all workers in the field will be prepped for following the job site’s standards. These best practices will help keep your project on schedule and on budget.
Invest in Compressing Your Construction Schedule
Technology is changing the construction industry. Delays are no longer an inherent issue for every project, and multi-trade layout does not need to take months. Companies investing in BIM-driven layout are compressing construction schedules despite a labor shortage and establishing a competitive advantage.
Secure your competitive advantage with Dusty’s FieldPrinter.