How Architects and Contractors Use BIM for Better Design
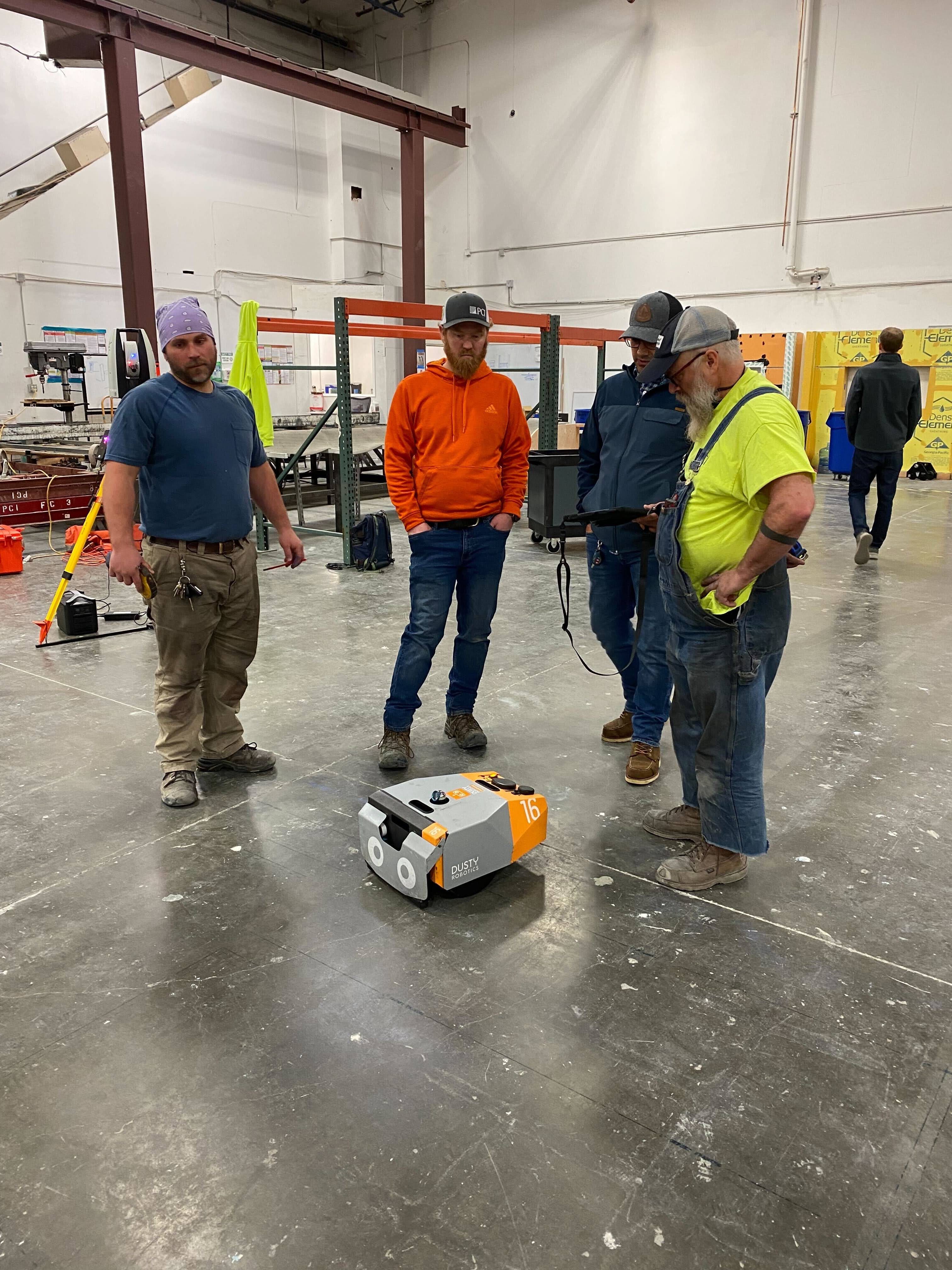
Designing commercial buildings can be a laborious and time-consuming process, especially when collaborating with multiple architects, engineers, contractors, and trades. Without a cohesive and flexible method for working together, important information can fall through the cracks before the foundation is even realized. Building Information Modeling (BIM) allows for real-time coordination throughout the planning, designing, and construction process.
In this blog, we’ll cover how architects and contractors can use BIM for better designs, the current challenges, and how the use of a BIM-to-Field layout is transforming the construction industry.
Using BIM, architects can create accurate 3D models of their designs, simulating exactly how a building will look and function once it’s completed. Most importantly, the contractors and other trades involved in the planning process can collaborate in real-time within the model. Each party involved has access to a unique “view” of the model in which they can create and modify their designs. The other collaborators can see these views and adapt their designs to better function holistically. As a result, critical issues or inconsistencies can be identified early on in the design process, instead of discovering unwelcome surprises in the field. BIM is a valuable method that enables projects to be completed faster and more efficiently. Likewise, architects and contractors have found several ways to use BIM to improve their projects. Here are a few examples:
- Cross-Trade Collaboration
Designing a building has a lot of moving parts, and without alignment, they can easily fall out of place. Since 3D BIM designs provide a centralized location for cross-trade collaboration, it’s significantly easier to track changes and progression.
- Custom Designs
With enhanced collaboration and accurate 3D representations of all aspects of the building, architects and builders are able to produce elaborate custom designs. Seeing these creative ideas come to life within a 3D model also allows users to identify changes that are needed to make the project possible. This visibility and collaboration are key to fostering the innovation and creativity that lead to unique and functional designs.
- Holistic Scheduling
BIM incorporates scheduling data for architects, as well as other trades involved. With complex and differing schedules for different aspects of design and construction, this visibility helps to share and maintain expected timelines.
- Quality Control
When designs are disparate and siloed, it’s difficult for architects and contractors to ensure the quality of the overall design. With BIM, architects can present the 3D design to the wider team for feedback, helping catch issues early on. Likewise, contractors can see how the different trades function together, preventing low-quality designs from moving into the layout process.
What are the Challenges of Using BIM?
As you’ve learned, BIM is a great way to design and plan complex commercial buildings. However, once these detailed and accurate BIM designs are complete, the layout on the construction site floor is typically done manually. This means that builders have to use measuring tape and chalk lines to lay out large commercial buildings. It also means that the detail and accuracy of the BIM designs can get lost in translation. Especially for intricate, curved designs and aligning multiple trades like drywall and MEP. Until now. With Dusty Robotics’ FieldPrinter, using an automated BIM-driven layout is possible.
What is a BIM-Driven Layout?
As opposed to manually measuring and marking layout, Dusty’s FieldPrinter autonomously prints the BIM model onto the construction site surface. This helps to bridge the gap between an architect’s design and the physical layout of the design in the field. For instance, with exact text labels and intricate lines printed for each trade involved, installation can proceed without ambiguity regarding the design intent. While using a BIM-driven layout is a relatively new innovation, it is already making a significant impact in improving the construction industry. Read on to learn more about the advantages of using BIM with BIM-to-field layout automation.
Advantages of Using BIM & BIM-Driven Layout in Construction
BIM has 6 associated Levels of Detail (LOD), with LOD 100 being the least amount of detail and LOD 500 being the most detailed. Within LOD 500, architects produce a highly realistic building model with accurate specifications regarding the design’s orientation, shapes, and quantities. In addition, trades fill out the framework information including structural, thermal, and electrical designs. At this level, there are also calculations for cross-trade interactions, as well as the building materials, dates of installation, and maintenance. Using BIM LOD 500 with a BIM-driven layout is the most comprehensive and beneficial process currently available for architects and contractors.
When LOD 500 is combined with a robotic BIM-to-Field layout, these highly-detailed and accurate BIM models are printed directly onto the construction site surface. Without error-prone and manual layout, it’s possible to preserve the accuracy of these collaborative BIM models. Architects are able to pursue increasingly complex and unique designs and benefit from their designs being constructed correctly on the first try. Not to mention, contractors benefit from the fully automated multi-trade layout, compressing schedules, saving skilled labor costs, and eliminating needless errors. In addition, all parties and trades succeed when these large-scale and complex projects are completed on time and within budget.
Let’s review the top 6 benefits of using BIM and BIM-to-Field layout for design and construction projects.
- Detect Issues Early
Issue detection is a critical, expensive, and high-stake process to get wrong throughout design and construction. When design problems are not identified until construction has started, they require redesign and rework which takes additional time, money, and labor. Notably, this can also lead to a claim or dispute being filed against the architect or engineer on the basis of a faulty element of design or an omission in the design. Claims can be complex and costly, so the earlier that issues can be detected, the better.
BIM 3D designs provide visibility into all of the proposed plans across trades, meaning it’s easier to see when certain design aspects are not going to be compatible. By identifying and resolving these issues in the design stage, the entire project is faster, cheaper, and let’s be honest, more pleasant for everyone involved.
- Enhance Accuracy
While architects can design beautiful and intricate features such as curved walls or custom light fixtures, their designs can get lost in translation if they are not laid out accurately and precisely. With a thin margin for error and expensive repercussions, it’s better to complete the layout accurately the first time. Using a robotic BIM-to-Field layout system guarantees accuracy. Dusty’s FieldPrinter can print all trades’ layout with 100% accuracy, making sure that all of the installed materials land where they need to go. Architects can see their designs come to fruition accurately, and contractors can rest easy knowing that crucial layout tasks were completed correctly and in record time.
- Reduce the Need for Skilled Labor
With an aging workforce and limited skilled labor available, 88% of construction companies have been unable to hire the skilled workers they need for a project. Likewise, 61% of construction projects end up getting delayed due to labor shortages. Slow construction progress and delayed schedules negatively affect everyone involved in a project, including architects, engineers, and contractors.
Using BIM with BIM-driven layout technology reduces the need for skilled labor in the field. With an automated and robotic layout, construction projects can stay on schedule without the need for skilled labor.
- Improve Scheduling
Scheduling large construction projects with several trades involved can quickly become complex. Expected timelines can get thrown to the wind, negatively impacting all of the other timelines involved. BIM helps to detail and share expected timelines for each aspect of a project, allowing for a more accurate schedule sequencing across trades. With clear and centralized scheduling for all trades, projects are more likely to follow the expected timelines. Moreover, when BIM scheduling is combined with the accuracy and speed of a BIM-to-field layout, installation can get started faster and without redundancies.
- Upgrade Sustainability
The most advanced level of BIM, level 6, uses multi-trade data to calculate the energy consumption of a building before it’s actually built. This innovative technology allows large-scale construction projects to track and follow energy efficiency standards. Likewise, more accurate and detailed energy consumption data helps companies pursue green building certifications. As sustainability becomes an increasingly influential aspect of business, the architects, engineers, and contractors that can help facilitate sustainable buildings will continue to benefit.
- Increase ROI
Lastly, using BIM and a BIM-driven layout can significantly cut costs and improve ROI. With early issue detection, accurate layout, faster installation, optimized schedules, and fewer resources required, large-scale construction projects can become substantially less expensive. Robotic BIM-driven layout is the future of the construction industry, and using this technology pays off.
Getting Started with BIM-Driven Layout
While BIM is immensely beneficial for architects and contractors, the true value is realized by automating the BIM-to-Field workflow during construction. With alignment between design and construction, complex and creative projects can be completed quickly and within budget.
Explore how Dusty can streamline your design and construction projects.