A Complete Guide to Digital Twins in Construction
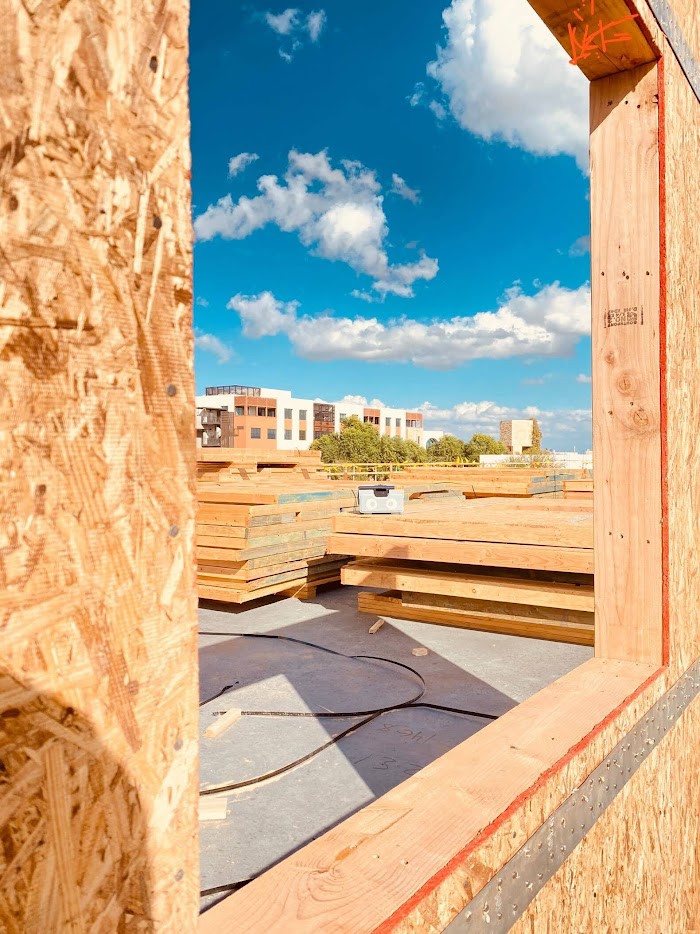
From early planning to long-term facilities management, digital twins in construction offer many advantages. Read on to discover how digital twins enable the simulation, real-time monitoring, and optimization of construction projects.
What Are Digital Twins?
A digital twin is a virtual replica of a physical structure, mirroring every detail through integrated 3D models, data, and simulations. These dynamic digital copies help construction companies optimize planning and execution. The technology allows you to visualize the final product even before the ground is broken, enabling paperless construction, clash detection, and constructability analysis. Later, during physical construction work, multi-trade layout technology, such as the Dusty Robotics Fieldprinter®, enables the digital twin data to be printed directly onto the construction site as a layout guide. For owners, digital twins are also a valuable resource that aids operations and maintenance after construction is completed.
The Applications of Digital Twins in Construction
Let’s take a look at how digital twins can be applied across the asset lifecycle.
- Design and Engineering: Digital twins enable virtual prototyping before construction starts. The digital twin simulation integrates architectural and engineering models to assess design feasibility, conduct Building Information Modeling (BIM) clash detection, visualize final products in 3D, and optimize the structure iteratively.
- Course of Construction: The digital twin mirrors real-time progress during construction using Internet-of-Things (IoT) sensors, drones, and subcontractor data. This is used for logistics planning, materials forecasting, workforce allocation, and tracking build status against project timelines.
- Operation and Maintenance: Post-construction, the digital twin transforms into an as-built digital record of the asset with all its data history. Facilities managers can leverage this "digital profile" for long-term maintenance, such as predicting equipment failures, optimizing energy consumption, tracking usage patterns, and running lifecycle analysis.
- Retrofits and Renovations: For existing buildings undergoing refurbishment, creating a digital twin with laser scanning and IoT data helps simulate retrofit options. Teams can model and visualize renovation sequences, augment virtual prototypes with product specs for upgrades, and validate constructability.
The Components of a Digital Twin
Digital twins integrate key technologies to enable advanced simulations and data-driven insights:
1. Building Information Modeling (BIM)
BIM refers to the creation of multi-dimensional CAD models before construction starts. It also provides a foundation for building digital twins. BIM models encode every detail in integrated 3D layers that include structural components, equipment specifications, spatial dimensions, materials, budgets, and work sequencing. This unified BIM representation forms a virtual prototype that mirrors all the intricate engineering plans and data points for the structure.
Digital twins then integrate BIM models and real-time site activity to produce dynamic virtual replicas that mirror every aspect of a building to create a single source of truth for construction, and later, for ongoing operations and maintenance.
Robotic technology such as Dusty’s FieldPrinter makes BIM-to-field layout possible by autonomously printing a full-scale BIM multi-trade layout onto the construction site surface, improving construction speed, efficiency, and accuracy, and preventing expensive rework.
2. IoT Sensors
A network of IoT sensors installed on the site, equipment, and materials tracks real-time progress and performance. This allows remote monitoring of construction status, asset health, logistics, and more. Digital twins sync with BIM models, updating them with as construction progresses. Over time, the data creates an advanced "digital profile" of the asset.
3. Data Integration and Machine Learning
BIM and IoT data, combined with cloud computing, enable automated analysis, insights, and machine learning. Cloud-based simulation platforms host the digital twin model and run complex analytical workflows. The model is accessible to any stakeholder through desktop or mobile dashboards.
4. Visualization and Virtual Reality (VR)
Advanced 3D visualization and VR environments help teams visually interact with the digital twin structures and construction sites in an immersive format. This creates intuitive experiences for design reviews, progress inspection, constructability analysis, and operations monitoring.
5. AI Algorithms
Integrating AI within the digital twin platform enables predictive insights about risks, issues, outcomes, maintenance needs, and so on. AI merges lifecycle data to forecast scenarios, prescribe solutions, and guide data-driven decisions.
What Are the Benefits of Using Digital Twins?
Digital twins help you optimize plans, improve decision-making, reduce errors, and enhance processes. They offer advantages at each phase of a construction project by bridging the physical and digital worlds, providing improved insights and performance.
Key benefits include:
1. Enhanced Visualization
Integrating digital twins with augmented and virtual reality tools enables immersive design reviews. This visualization helps stakeholders gain a deep understanding of design plans, construction sequences, and final products. It also allows them to identify clashes between architectural, structural, and MEP models before any physical work begins.
2. Seamless Collaboration
Digital twins enhance coordination across large, complex projects by establishing a common data environment for all stakeholders. With the entire project timeline mirrored digitally, teams stay aligned on schedules, milestones, contingencies, and progress.
3. Optimized Planning
Virtual Design and Construction (VDC) enables assessing various design and build scenarios to optimize sequencing, logistics, budgets, and resource allocation per project needs. Automated multi-trade layout with Dusty Robotics FieldPrinter maximizes the benefits of VDC, automatically printing the coordinated model, layout, and installation on-site with the same accuracy as the optimized VDC model. Clash detection functionalities also minimize errors and delays due to rework.
4. Real-Time Tracking
Integrating IoT sensor data enables the digital twin to mirror real-time site conditions and construction status. Project managers can thus track progress remotely without being physically present. This proactively mitigates delays, change orders, or cost overruns.
5. Future-Ready Platform
The digital twin is a virtual representation that evolves over the asset's lifespan, providing actionable insights for operations, maintenance, and more. It forms the foundation for leveraging future innovations like robotics, augmented reality, and artificial intelligence.
Implementing Digital Twins in Construction Projects
The effective use of digital twins for insights and oversight requires careful planning and execution. Let’s take a closer look:
1. Establish Project Objectives and Requirements
First, define goals and targets for deploying digital twins. This could be improved on-site safety, faster project delivery times, reduced rework percentages, or lower change order costs. Outline requirements for the digital twin solution, including:
- BIM integration for foundational 3D models
- Sensor connectivity protocols for on-site data
- Data storage needs and analytics engines
- Advanced functionalities for sequencing and clash detection
- Ease-of-use for teams in model updates and report access
This establishes clarity on the role of digital twins in your workflows.
2. Select the Right Technologies
Next, assess hardware and software options from market-leading digital twin solutions, such as Siemens, GE, or IBM. Audit equipment like drones, LiDAR, and CCTV for data capture. Evaluate analytics engines, visualization interfaces, and simulation toolsets.
Prioritize the functionalities needed, like clash detection, construction sequencing, or resource planning. Select platforms that balance customizability and pre-built integration.
3. Integrate Digital Twins Into Existing Workflows
The digital twin platform should link real-time data with design information from BIM and other systems. API integration and end-point connectors are vital for unified data access.
Clearly map information flow across the technology stack to minimize disruption to legacy processes. Assign asset hierarchy and identity tags for equipment, materials, and building components to sync across virtual and physical dimensions. Test integrations thoroughly before live deployment.
4. Train Employees on Digital Twin Usage
User adoption issues can limit the ROI from digital twins. Provide training workshops for employees on updating data, leveraging reports, and collaborating effectively.
5. Ensure Governance and Multi-Stakeholder Collaboration
Define protocols for model ownership, access controls, change approvals, and data security at the start of your digital twin implementation. Introduce information governance policies around compliance, quality controls, and master data.
Promote collaboration by providing interactive access to digital twin analytics and work-in-progress models to all stakeholders. This gives visibility across the construction timeline for better resource planning.
How Do You Overcome the Challenges of Using Digital Twins?
Digital twins bring value but have some barriers to adoption. Let’s look at these obstacles and how you can tackle them:
- Data Security Concerns: Digital twins ingest vast amounts of data from BIM, IoT, drones, and more. This raises valid data privacy and security concerns that must be addressed through encryption, access controls, and compliance audits.
- Interoperability Issues: Interoperability and standardization challenges arise when combining data from different systems. Robust API integrations across tools are vital for real-time data availability.
- Initial Outlay Considerations: As with the adoption of all new technologies, implementing digital twins has some upfront costs, including the purchase and installation of IoT sensors, analytics tools, and simulation platforms.
- Organizational Change Management: Adopting digital twins and robotics requires evolving mindsets around technology, data, and collaboration. Leadership must champion digital transformation objectives and incentivize usage. Aligning training programs with performance evaluation helps drive adoption at scale. These steps help overcome barriers to adopting cutting-edge technologies.
Leveraging Digital Twins With the Dusty Robotics FieldPrinter
Digital twins improve construction performance by combining virtual and physical data and providing digital continuity. For companies exploring digital transformation, the Dusty Robotics FieldPrinter serves as an ideal launchpad for implementing digital twin capabilities on-site. The platform has these key features:
- Flawless Build Execution: Dusty's FieldPrinter replicates ultra-accurate BIM models directly on-site to guide construction teams, ensuring flawless execution as per designs.
- Links to Digital Twins: By printing layout from all trades across worksites, Dusty creates accurate-to-the-model links between virtual prototypes and physical builds.
- Validates Simulations: Teams can instantly validate digital twin simulations and virtual walkthroughs against Dusty's on-the-ground prints.
- Foundational Layer: Dusty paves the way for further IoT, predictive analytics, and lifecycle modeling capabilities downstream.
Learn more about how the FieldPrinter automated layout solution helps you print digital twins data right on the construction site surface, improving accuracy, boosting efficiency, and cutting rework.